3 Things to Know About Epoxy-Coated Rebar
- By Admin
- •
- 12 Feb, 2019
- •
This is a subtitle for your new post
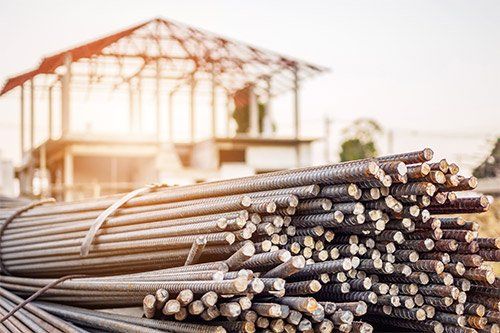
Concrete has a natural degree of strength and hardness that makes it one of the most popular paving materials. Yet as time goes on, concrete may still suffer from crumbling, cracks, and other forms of damage. Load-bearing concrete stands an even greater chance of suffering premature degradation.
To boost the strength of concrete, contractors often bolster the slab with steel reinforcing bars - or rebar for short. Numerous different types of rebar exist, each of which possesses a unique set of advantages. This article outlines four key things to know about one of the most popular varieties of rebar: epoxy-coated rebar.
1. Epoxy-Coated Rebar Protects Against Corrosion
The most basic and inexpensive form of rebar consists of simple steel bars. While effective at boosting internal strength, plain steel rebar often falls prey to corrosive forces as times goes on. As rust forms on outside of the embedded rebar, it exerts an increasing amount of pressure on the surrounding concrete.
Such internal pressure can cause the concrete slab to spontaneously crack, while also making the concrete must more vulnerable to damage caused by blows and compressive forces. The surface of the concrete may develop patches of spalling, creating rough, unattractive areas as the concrete chips and flakes away.
Epoxy-coated rebar prevents corrosion and the problems that it causes. Manufacturers cover the entire bar of rebar in a coating of epoxy. This water-impermeable layer minimizes the chances that corrosion will take hold of the rebar.
2. The Epoxy Coating Must Remain Undamaged for Optimal Results
The effectiveness of epoxy-coated rebar depends on the integrity of the epoxy layer. If the epoxy becomes chipped, torn, or otherwise damaged, the underlying steel becomes exposed. Even a tiny portion of damage allows corrosion to set in. Once rust has begun forming, it works its way under the remaining epoxy, thus undermining the coating entirely.
For this reason, contractors must exert care when transporting and installing epoxy-coated rebar. Likewise, contractors must show care regarding where and in what conditions the rebar is stored. The epoxycoating remains quite vulnerable to ultraviolet light, and will quickly degrade when left exposed to UV for too long. When stockpiling epoxy-coated rebar outdoors, therefore, contractors should always cover it with a UV-impermeable tarp or other form of protection.
Another critical factor involves installation temperature. Handling epoxy-coated rebar in temperatures below 50 degrees Fahrenheit can cause the epoxy coating to crack.
3. Contractors Can Repair Damaged Epoxy Coating
To ensure long-term viability, workers should inspect every piece of rebar before placing it in a reinforcing framework. While this process can be somewhat time consuming, an upside does exist: contractors can often repair any pieces of rebar whose epoxy coating has suffered damage.
A contractor repairs epoxy-coated rebar using an appropriate patching material. The most common repair material involves a two-part epoxy coating, which the worker paints onto the rebar. First, however, the worker must thoroughly remove any corrosion present on the damaged area.
4. Epoxy-Coated Rebar Has Universal Applications
When correctly handled and installed, epoxy-coated rebar can benefit a wide variety of different concrete projects. The corrosion-resistance of epoxy-coated rebar makes it especially useful for structures located in marine environments, as well as for structures that regularly receive applications of deicing salts.
For instance, parking decks in the United States suffer roughly 600 million dollars worth of damage every year as the result of deicing salts. The use of epoxy-coated rebar in such structures can greatly reduce the cost of future repairs. For more information about the installation of epoxy-coated rebar, please contact the concrete pros at Jimenez Concrete Inc. We'll be happy to help you with any of your rebar needs.
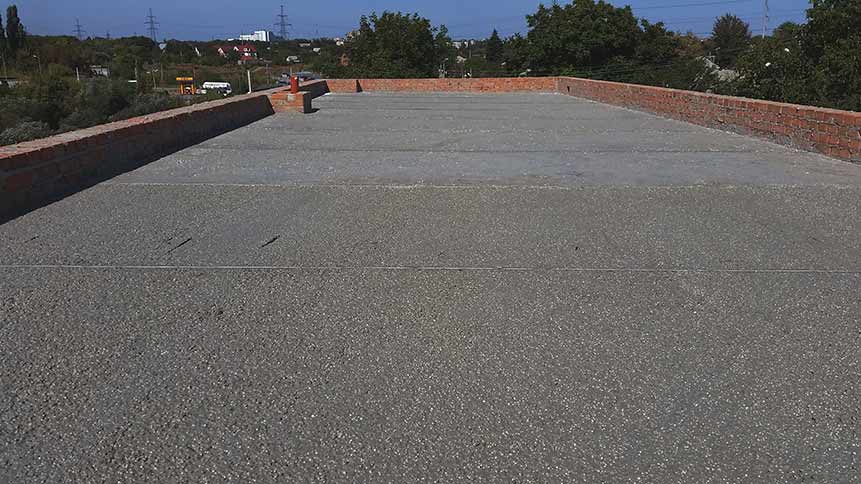
Cellular concrete consists of a mixture of water, cement, and pre-formed foam. Contractors and manufacturers sometimes refer to cellular concrete as foamed concrete. Because cellular concrete forgoes stone aggregate, and because the foam introduces a higher ratio of air, it has a much lower density than traditional concrete.
Cellular concrete possesses numerous benefits when it comes to certain types of building and restoration projects. Unfortunately, many people still fail to understand just what makes cellular concrete so special. This article seeks to increase your knowledge of the contemporary concrete world by outlining four key advantages of cellular concrete.
1. Lighter Weight
The defining feature of cellular concrete is its relatively high air content. The foam leaves behind evenly distributed cells of air in the hardened concrete, and the air may account for up to 80 percen t of cellular concrete's volume. That said, a contractor can carefully adjust the precise ratio of foam introduced to control the amount of air and end up with a desired density.
As you can imagine, the more air cellular concrete contains, the lighter it will be. Generally speaking, however, virtually all cellular concrete weighs less than its traditional equivalent. This characteristic gives it a distinct advantage when it comes to certain types of construction or repair tasks.
Cellular concrete allows builders to stay within strict weight management limits for certain types of buildings. Walls and floors constructed from cellular concrete place a much smaller load on a building's foundation, often allowing builders to construct taller structures. The light weight means it can even be used as a roofing material.
2. Better Thermal Insulation
The high air content of cellular concrete also produces a drastic effect in terms of thermal insulation. Just as with density, insulating power relates directly to the proportion of air in the concrete — more air increases the insulating power. As a result, structures built using cellular concrete tend to exhibit much better energy efficiency.
Manufacturers test a building material's insulating power according to R-value Higher R-values indicate a greater degree of insulation. One inch standard concrete, which has a density of 150 pounds per cubic foot, has an R-value of just 0.07. Cellular concrete, at the extreme end of the spectrum, may have R-values as high as 2.0 per inch
.
3. Improved Fire Resistance
All concrete possesses a natural degree of fire resistance. Yet not all concrete can withstand the same temperatures or for equal lengths of time. The same insulating properties that make cellular concrete such a great choice for energy efficiency also give it an improved ability to resist heat transfer, thus making it harder for fire to spread throughout a building.
Standard concrete that has been reinforced with rebar or other internal steel elements has a greater susceptibility to fire. As the heat from especially intense fires passes into the concrete, the metal rebar expands, creating internal stress. As a result, the concrete often succumbs to spalling damage.
To combat this weakness, concrete manufacturers often add monofilament polypropylene fibers to the mix. While effective, this strategy can drive up the cost of the concrete. The excellent insulating properties of cellular concrete offers an alternative way to resist spalling. Cellular concrete is also less likely to explode as the result of exposure to a high energy flame source.
4. More Cost-Effective
Most cellular concrete contains an ingredient known as fly ash, which promotes a greater degree of internal strength. Fly ash replaces some of the cement that would otherwise be used in the mix. This replacement tends to bring down the overall cost of the concrete, since fly ash is an industrial waste product that can be acquired for a fraction of the cost of cement.
Cellular concrete has become an increasingly popular building choice, thanks to its wealth of undeniable benefits. For more information about whether cellular concrete would make a good choice for your next construction project, please contact the pros at Jimenez Concrete Inc.
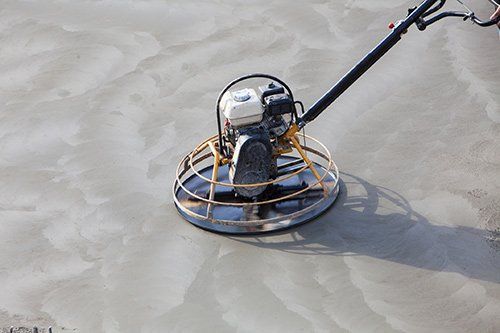
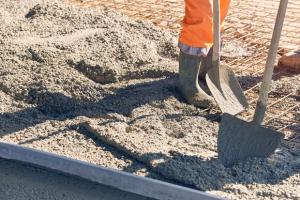
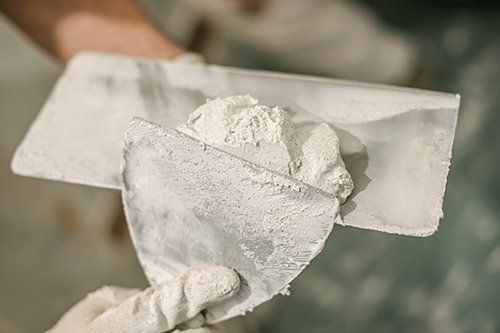
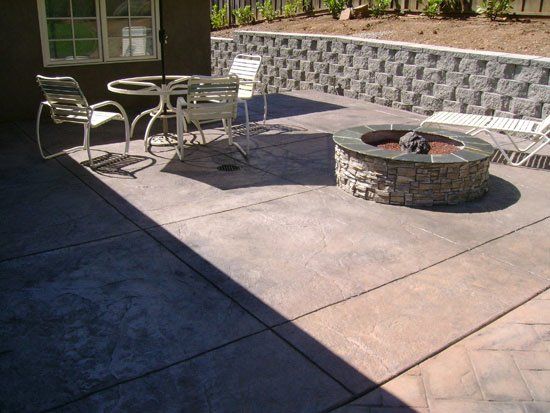
It takes do-it-yourselfers longer to smooth and level concrete because they are not used to doing this task.
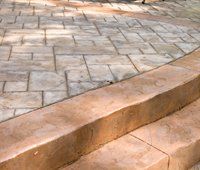
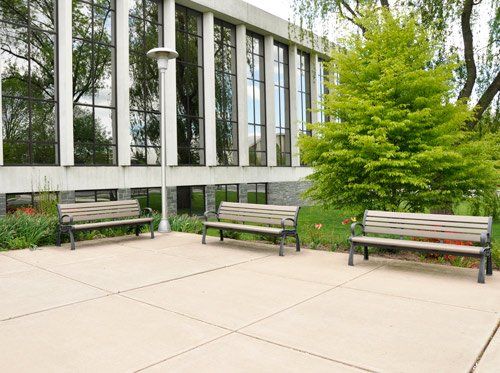