Signs That Your Garage Floor Needs Replacing
- By Admin
- •
- 08 Apr, 2019
- •
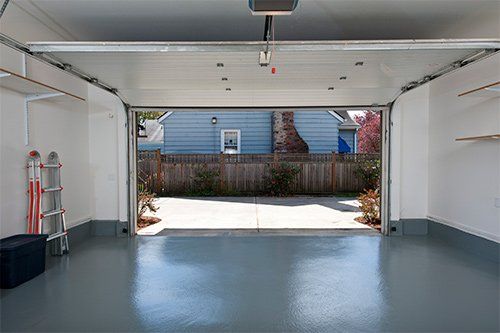
The life of a garage floor is not an easy one. This concrete floor is continually subjected to heavy vehicles, chemicals, oil, dirt from outside, and in some cases, extreme temperature fluctuations. As a result, the floor can crack, pit, or even begin to sink after years of use. If your garage floor is old and damaged, you may need to replace it.
Replace or Repair Your Garage Floor
You may be tempted to try and repair the floor of your garage if you start to see damage to the floor, but the reality is, the floor endures too much abuse for repair to stand up well over time. You may be able to fix it, but in time, the floor is likely to begin showing damage again. The best solution is to replace the floor entirely. It is a big job, but when done right, the floor will last for many more years.
Signs to Watch For
You can watch for some key signs that will indicate a problem with the floor and let you know it is time to replace it. If you pay attention to these signs, you can replace the floor early, before it causes other problems.
Cracks in the Surface
Once the floor in your garage has started cracking, there is not much you can do to repair it. You can patch the cracks with concrete, but the likelihood of it lasting for more than a couple years is pretty low. The new concrete is not going to bond with the old concrete as well, and if there is even a small crack in the surface, water will find its way in and do more damage under the surface, where you can't see it.
Pitting on the Surface
Over time, chemicals like oil, antifreeze, and gasoline will damage the concrete. The surface of the floor may develop pits or small holes in it, and over time those holes will get bigger, making your smooth concrete floor rough. The concrete may start to deteriorate and come loose in small chunks, which will get worse if not dealt with.
Uneven Floors
Another concern you should watch for is the surface of the floor starting to shift and become uneven. If the floor begins to sink, the ground under it is more than likely settling. The floor may stop moving if the soil settles completely, but if it doesn't, the concrete will eventually crack or break.
Uneven floors can make it hard to use the garage as well. Things like tools boxes on wheels may begin to move or not stay in place, and if the floor sinks near the entrance, it can make it difficult to get your car in and out of the garage.
Cost of Replacement
A lot of factors go into setting the price of replacing a garage floor. On average, the cost will fall somewhere between 6 and 15 dollars per square foot to replace. The cost may vary from place to place and company to company, so call some local contractors in your area to get a more accurate price.
One thing to keep in mind, the cost of the floor often includes demolishing and removing the old cement floor, prepping the ground under it, installing rebar or other reinforcing materials, and pouring the floor. For maximum durability, you may want to consider coating the floor with an epoxy or sealing it to keep chemicals, dirt, and other contaminants off the concrete.
Jimenez Concrete Inc. has been in the concrete business for many years and has a staff with many years of experience working with concrete. We have the tools and expertise to replace your garage floor adequately so you will have many years of service from it. Give us a call so we can come and give you an estimate today.
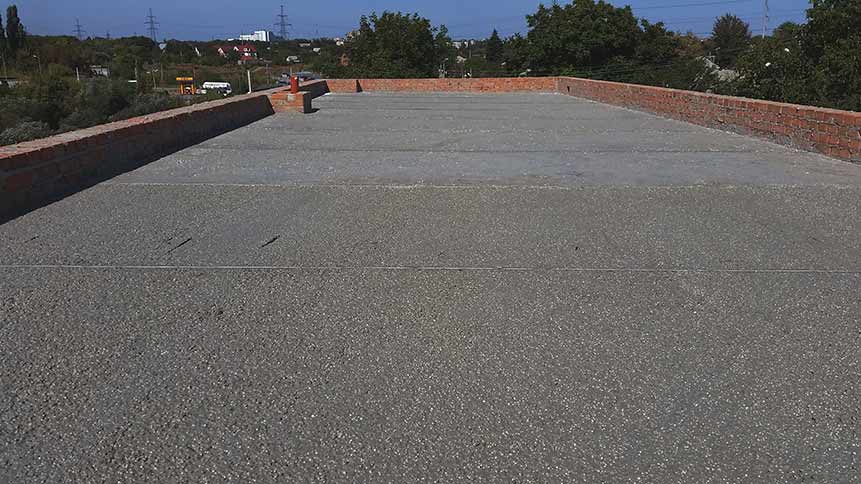
Cellular concrete consists of a mixture of water, cement, and pre-formed foam. Contractors and manufacturers sometimes refer to cellular concrete as foamed concrete. Because cellular concrete forgoes stone aggregate, and because the foam introduces a higher ratio of air, it has a much lower density than traditional concrete.
Cellular concrete possesses numerous benefits when it comes to certain types of building and restoration projects. Unfortunately, many people still fail to understand just what makes cellular concrete so special. This article seeks to increase your knowledge of the contemporary concrete world by outlining four key advantages of cellular concrete.
1. Lighter Weight
The defining feature of cellular concrete is its relatively high air content. The foam leaves behind evenly distributed cells of air in the hardened concrete, and the air may account for up to 80 percen t of cellular concrete's volume. That said, a contractor can carefully adjust the precise ratio of foam introduced to control the amount of air and end up with a desired density.
As you can imagine, the more air cellular concrete contains, the lighter it will be. Generally speaking, however, virtually all cellular concrete weighs less than its traditional equivalent. This characteristic gives it a distinct advantage when it comes to certain types of construction or repair tasks.
Cellular concrete allows builders to stay within strict weight management limits for certain types of buildings. Walls and floors constructed from cellular concrete place a much smaller load on a building's foundation, often allowing builders to construct taller structures. The light weight means it can even be used as a roofing material.
2. Better Thermal Insulation
The high air content of cellular concrete also produces a drastic effect in terms of thermal insulation. Just as with density, insulating power relates directly to the proportion of air in the concrete — more air increases the insulating power. As a result, structures built using cellular concrete tend to exhibit much better energy efficiency.
Manufacturers test a building material's insulating power according to R-value Higher R-values indicate a greater degree of insulation. One inch standard concrete, which has a density of 150 pounds per cubic foot, has an R-value of just 0.07. Cellular concrete, at the extreme end of the spectrum, may have R-values as high as 2.0 per inch
.
3. Improved Fire Resistance
All concrete possesses a natural degree of fire resistance. Yet not all concrete can withstand the same temperatures or for equal lengths of time. The same insulating properties that make cellular concrete such a great choice for energy efficiency also give it an improved ability to resist heat transfer, thus making it harder for fire to spread throughout a building.
Standard concrete that has been reinforced with rebar or other internal steel elements has a greater susceptibility to fire. As the heat from especially intense fires passes into the concrete, the metal rebar expands, creating internal stress. As a result, the concrete often succumbs to spalling damage.
To combat this weakness, concrete manufacturers often add monofilament polypropylene fibers to the mix. While effective, this strategy can drive up the cost of the concrete. The excellent insulating properties of cellular concrete offers an alternative way to resist spalling. Cellular concrete is also less likely to explode as the result of exposure to a high energy flame source.
4. More Cost-Effective
Most cellular concrete contains an ingredient known as fly ash, which promotes a greater degree of internal strength. Fly ash replaces some of the cement that would otherwise be used in the mix. This replacement tends to bring down the overall cost of the concrete, since fly ash is an industrial waste product that can be acquired for a fraction of the cost of cement.
Cellular concrete has become an increasingly popular building choice, thanks to its wealth of undeniable benefits. For more information about whether cellular concrete would make a good choice for your next construction project, please contact the pros at Jimenez Concrete Inc.
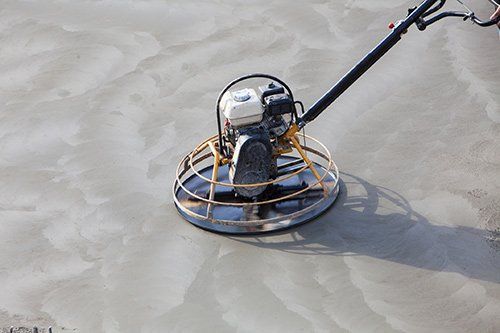
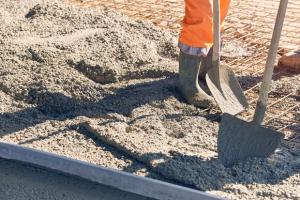
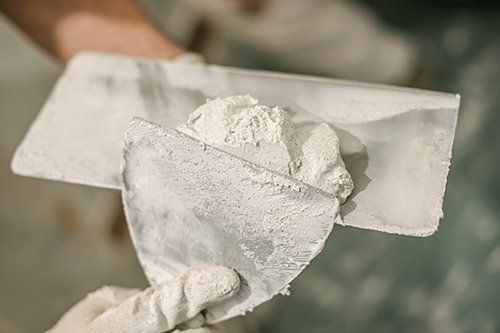
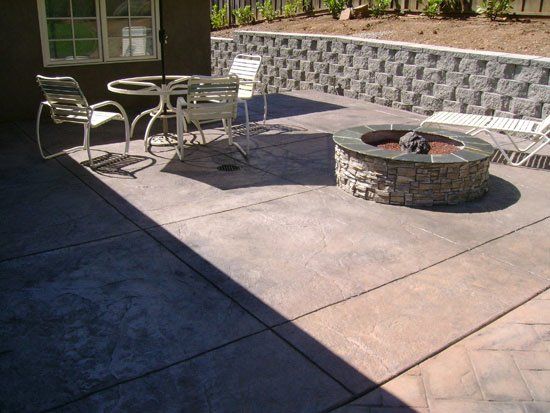
It takes do-it-yourselfers longer to smooth and level concrete because they are not used to doing this task.
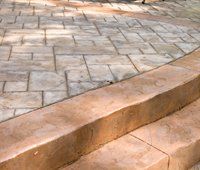
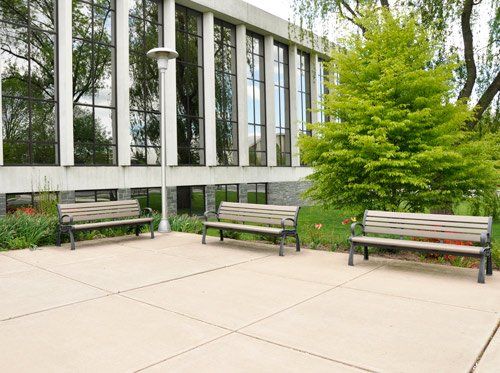